Key Takeaways
-
Concrete resurfacing is an affordable and durable solution to restore the look of your patio, walkway and other surfaces. If well cared for and maintained, it holds up well beyond 25 years!
-
The process begins with intense surface preparation. Next, we start the resurfacing process with advanced materials such as acrylic coatings, microtoppings or Acrylic systems to provide aesthetic value along with protected strength.
-
Resurfacing can create vibrant streets. Resurfacing offers an incredible amount of design flexibility. Select from stamped overlays and staining techniques that mimic the appearance of expensive materials, or design custom looks to fit any aesthetic.
-
Just like any concrete surface, it’s important to uphold regular maintenance for resurfaced concrete surfaces. Regularly cleaning, sealing, and making timely repairs will make them look beautiful and last much longer.
-
In Palm Beach and Broward, it is important that the materials used are weather and salt resistant. These materials continue to prove instrumental in combating the obstacles presented by extreme humidity, coastal salt exposure, and intense thermal cycling.
-
Working with experienced contractors who understand local regulations and environmental considerations ensures compliance, quality, and eco-friendly practices for resurfacing projects.
Concrete resurfacing in Palm Beach and Broward offers a highly effective method for restoring tired, worn surfaces. So, you can update your area without requiring a complete tear out.
Step one, we put down a long-lasting overlay right over the original concrete. This provides it with a smooth, fresh look and feel, improving both its usability and aesthetic. Resurfacing is perfect for addressing cracks, fading, and surface wear on driveways, patios, and pool decks.
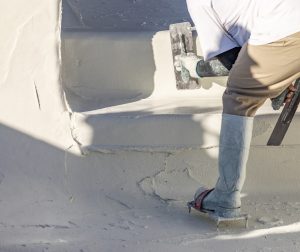
It gives you the ability to incorporate a unique design or hue that’s ideal for your aesthetic. The hot Florida sun takes its toll. By opting for superior materials, you’ll increase your concrete’s durability in the face of heat and humidity, ensuring a longer-lasting surface.
For homeowners and businesses alike, this solution is both budget-friendly and time-efficient, providing a beautiful finish with little disruption. Innovative solutions customized to your unique challenges drive sustainable outcomes.
What is Concrete Resurfacing?
Concrete resurfacing is an affordable, durable, and beautiful solution to renewing tired, outdated, or damaged concrete surfaces. Resurfacing restores the original concrete surface with a new layer of material, creating a smooth, clean appearance. This approach eliminates the expense of removal and replacement of the full slab.
This approach brings back beauty and usability to areas such as patios, walkways, and driveways. When done right, resurfaced concrete can last more than 25 years with regular maintenance. This robustness translates to dollars and cents for property owners, making it a smart, cost-effective choice.
1. Define Concrete Resurfacing Process
Detailed surface preparation is the first step to successful concrete restoration with resurfacing. Cleaning the surface provides a removal of oil, dirt, and debris, while patching cracks or holes provides a smoother surface for a stronger bond.
After thorough prepping, a highly specialized resurfacing compound—typically made of a mixture of cement, sand and polymer additives—is poured down. This combination helps to create a highly durable, crack-resistant surface.
Once applied, the surface is smoothed and can be further tailored with textures, colors, or patterns as you wish. Finally, a sealant is painted over the resurfaced pavement to provide protection against tire traffic and the elements.
2. Why Choose Resurfacing?
Cost-effective resurfacing is rather astounding when looking at it next to full concrete replacement. It provides aesthetic flexibility, enabling resurfaced surfaces to mimic luxurious materials such as stone or tile.
Concrete resurfaced areas are extremely low maintenance, requiring regular cleaning and resealing at most to keep them looking beautiful.
3. Recognize Signs for Resurfacing
When you see cracks, discoloration, uneven patches, or pooling water it’s time to think about resurfacing. Consistent inspections provide an opportunity to notice early signs of deterioration to get ahead of permanent damage and expensive fixes.
Explore Resurfacing Methods
Concrete resurfacing is an efficient, affordable, and flexible solution for restoring old, damaged concrete. For both homeowners and businesses in Palm Beach and Broward, understanding the available methods ensures a tailored solution that meets durability and aesthetic goals.
Acrylic Concrete Coating Systems
Acrylic coatings offer a high level of protection and beautification for concrete. This combination of systems creates a durable, weather-resistant surface, making them perfect for outdoor, exposed patios or driveways.
Preparation for the application includes cleaning the surface, priming, and many layers of acrylic, all with drying times of 24-48 hours in between. Available in a wide range of colors and textures, acrylic coatings can imitate traditional natural finishes or introduce bright, contemporary patterns.
Applying Microtopping Solutions
Microtopping, called micro screed, is a direct-applied thin overlay used to rejuvenate or restore old concrete. That makes it an ideal candidate for smooth, durable surfaces in interior spaces such as kitchens or open-concept living areas.
Microtoppings set durable bonds to existing concrete, providing creativity and contrast with myriad colors, designs, and textures. Customization goes far beyond standard color pigments and can produce elaborate stenciled patterns, resulting in one-of-a-kind finishes catered to individual preferences.
Concrete Staining Techniques Explained
Staining is a popular develop concrete resurfacing method due to its acid-based or water-based options. Acid stains produce rich, natural, variegated tones, and water based stains are available in more vivid, consistent shades.
This technique creates visual depth, movement and artistic flair to patios and interior floors.
Polished Concrete Finishes
Polishing creates very smooth, reflective surfaces. This minimal, easy-care solution to luxurious commercial lobbies or contemporary residences combines resiliency with a surprising amount of visual punch.
Palm Beach & Broward: Local Factors
Concrete resurfacing in Palm Beach and Broward areas demands a complex understanding of the specific environmental factors at play. The regional climate, soil composition, and proximity to the coast all play significant roles in determining the materials and methods needed for durable and effective resurfacing.
These local realities have a major effect on the durability, usability, and upkeep of concrete in these communities.
Weather Conditions Impact Resurfacing
In 2022, high temperature and humidity—conditions that are typical for Palm Beach and Broward—have been known to compromise the structural integrity of concrete. Continual moisture exposure can cause cracking or spalling, and heat instantly wears down the surface.
Especially in coastal regions, choosing weather-resistant materials can make the difference between a space protected from the damage of a tropical storm or sudden downpour. In particular, timing on resurfacing projects is key.
Plan them in drier months such as late fall or winter to limit moisture exposure while curing, which results in better outcomes. As an illustration, a resurfaced flat driveway done correctly with $200-$400 worth of materials might reasonably be expected to last 8-15 years with good maintenance practices.
Soil Composition’s Role
The region’s sandy and often unstable soil can play a role in how well concrete holds up. If drainage is poor, cracking and settling are even worse, so good drainage solutions are even more important.
Taking stock of soil conditions before resurfacing is a great step to tackling these challenges right off the bat. For example, applying specialty coatings or underlayment can help prevent shifting from poor rib soil bases, increasing stability for the surface.
Combatting Coastal Salt Exposure
Salt air significantly accelerates corrosion, particularly in unprotected concrete. Salt-resistant materials like Acrylic coatings apply a tough barrier against this corrosive effect.
Proper maintenance, especially periodic sealing, helps fight the effects of salt, extending a surface life by as much as 50 percent.
Humidity and its Effects on Concrete
High ambient humidity can lead to moisture-related issues, like mold growth or inconsistent curing. When used with proper curing techniques and breathable coatings that allow any trapped moisture to escape, they prevent costly long-term damage while delivering excellent surface quality.
Projecting Resurfaced Concrete Lifespan
When resurfaced concrete is done right, it can hold up for a decade and a half or more. Climate, foot traffic, and quality of materials are all factors that contribute to how long something will last.
Consistently cleaning and sealing your surfaces will preserve their beauty for years to come. Make small crack repairs quickly to prolong the life of the crack and mitigate your investment.
Factors Influencing Overall Value
The value of resurfacing is enhanced by professional supervision and high-quality materials, which can maximize design flexibility. Ornamental surfaces, such as stamped patterns or colored overlays, increase the visual attractiveness of a given property.
Using superior materials will improve durability, combined with skilled contractors focused on exact application, which means less repairs down the road. These compactness and shading elements together increase property value and curb appeal, providing many years of payoff.
Maximize Resurfaced Concrete Lifespan
Maximizing the lifespan of resurfaced concrete takes a multi-faceted approach that includes proactive maintenance, protective treatments, and making timely repairs on distressed pavement. Embrace proactive approaches that guard against the deleterious effects of aging and harsh weather on Palm Beach and Broward’s concrete surfaces. Save their looks while dealing with their home region’s cruel climate!
Below, we highlight some essential practices you can follow to help maximize the durability and longevity of your project’s outcome.
Implement Regular Cleaning
-
Sweep the surface at least weekly to remove dirt, sand and debris.
-
Clean regular dirt and debris with a gentle pressure washer or high-pressure garden hose monthly.
-
Don’t use abrasive chemicals, rather pH neutral cleaners made specifically for use on concrete.
Regular cleaning prevents the buildup of dirt and debris that can wear down the concrete over time. Choosing the right cleaning products is very important to avoid discoloration or compromising the strength of the resurfaced layer. For instance, basic or acidic solutions may put you at risk of harming the floor finish.
While the frequency of cleaning will depend on the site, every month deep cleaning is strongly encouraged in high-traffic areas to keep the surface looking and performing its best.
Seal and Protect the Surface
Specifically, sealing resurfaced concrete adds a protective barrier that helps prevent damage caused by moisture intrusion, UV rays, and stains. For additional water protection, penetrating sealers are effective, and for color and sheen, acrylic sealers beautify the surface.
Resealing every 2-3 years ensures the surface remains protected and reduces the risk of cracks or wear caused by environmental factors.
Promptly Address Cracks and Damage
Repairing cracks when they are small prevents moisture intrusion and subsequent damage. Epoxy or polyurethane fillers will work for minor cracking and would need patching compounds for surface damage.
Ensuring a long-lasting surface, timely repairs maintain the surface’s structural integrity and avoid more expensive replacements.
Environmental Considerations
As the region moves forward with concrete resurfacing in Palm Beach and Broward, there’s a huge opportunity to prioritize environmental considerations along with durability. Implementing environmentally-friendly practices strengthens your commitment to sustainability. It makes your work last longer and your projects better.
By making environmentally friendly decisions a priority, we can lessen waste, harmful emissions and build healthier communities.
Eco-Friendly Material Choices
The use of a wider variety of green resurfacing materials and coatings to accomplish sustainability objectives is available on the market. Recycled content choices such as recycled aggregates, fly ash, and slag cement offer long-lasting solutions that help steer projects away from virgin material extraction.
For instance, substituting recycled concrete keeps material out of landfills with a long track record of successful and safe structural replacements. Florida’s local suppliers, such as ACG Engineering Services, provide these green materials right on their doorstep.
They purposefully engineer these constructions to endure the area’s harsh environment. When you source from your community, you reduce transportation emissions. This contributes to sustainable development in an even broader way.
Sustainable Resurfacing Practices
Making sustainable resurfacing the norm starts with smart planning. To prevent the problem of overordering, prioritize accurate material estimation. Utilize methods such as overlay systems to minimize use of new materials.
Waste should be minimized. Any excess debris could be reused for base layers or other construction uses. High-efficiency equipment and water recycling systems further prevent waste and conserve our planet’s resources, allowing us to maintain quality that is environmentally friendly.
Consideration of these elements during design and construction will maximize sustainability and long-term performance.
Minimizing Environmental Impact
Minimizing the carbon footprint requires careful planning, like using low-VOC sealers, which lead to better indoor air quality. The Environmental Protection Agency (EPA) highlights the great risks posed by particulates emitted during construction.
When you buy more local and eco-friendly products, you’re addressing those environmental issues directly. It further strengthens regional economies and reduces emissions associated with long-distance transportation.
Common Issues & Solutions
Concrete resurfacing in Palm Beach and Broward presents a different set of challenges owing to climate and environmental conditions. Catching and repairing these problems properly is key to ensuring a lasting fix and keeping these vital connections looking good and working well. Here, we take a deep dive into the biggest issues and the hands-on solutions.
Preventing Cracking and Delamination
Cracking and delamination frequently happen if the substrate is improperly prepared. An infection enters through the skin, and concrete surfaces that are already damaged, dirty, or have a compromised structural integrity do not provide a good adhering base layer for the resurfacing. Changes in temperature can create more expansion and contraction, resulting in cracks.
To avoid this from happening, make sure the surface receives prior cleaning, repair, and priming before your paint goes down. Employing quality materials created with thermal stability in mind can greatly minimize those risks. Regular maintenance, like sealing the surface every few years, helps protect against moisture and wear, minimizing the likelihood of cracking over time.
Addressing Uneven Surfaces
Uneven surfaces are an aesthetic issue and can be a functional liability. They usually result from failure to properly prepare for or allow for settling of the base layer. Recognizing low spots or bumps in advance is key, something you can do with a straightedge or laser level.
When used in conjunction with resurfacing, self-leveling compounds can provide a nice, smooth base. With proper finishing techniques, like troweling, consistent uniform thickness can be achieved. Installation of proper drainage systems helps keep water from pooling, which can erode the surface and lead to future bumps and dips.
Managing Moisture Problems
Moisture is a huge problem, especially in coastal areas like Palm Beach and Broward. It can adversely affect connected materials, weaken bonds, and result in premature failure. Using a vapor barrier prior to resurfacing prevents moisture from coming in.
Once the surface receives its final treatment, using waterproof coatings and sealants protects it even more. Choosing durable, moisture-resistant materials made for wet climates helps build for the long term and avoid future damage.
Choosing a Qualified Contractor
Choosing the right concrete resurfacing contractor is essential to getting lasting, quality results. You want someone who delivers quality work every time. A qualified contractor ensures expert craftsmanship. They save you money now and help you avoid expensive maintenance problems down the line.
Plus, local contractors are familiar with all the unique environment conditions specific to Palm Beach and Broward County. They’re particularly useful because they know how to navigate regional challenges, such as humidity and temperature swings that can shorten the lifespan of concrete.
Check References and Reviews
Determine contractor reputation by checking references, past work, and online reviews. Pay attention to five star ratings, especially for stamped concrete work as this shows a proven track record of adhering to high quality standards.
Communicating with previous clients will shed light on the contractor’s communication, quality of work, and capacity to meet deadlines. Knowing this information will put you at ease as you make your decision.
Get Multiple Bids and Estimates
Collecting multiple estimates allows you to get a feel for the price and services available. Carefully compare the contents of each bid. Look for warranties, cleaning processes (pressure washing only at 2,000-2,500 PSI), and other services such as free estimates.
Taking the time for a side-by-side comparison guarantees you the best value and can save you 50-80% over the cost of replacement.
Inquire About Warranties and Guarantees
Make sure your contractor provides a warranty on workmanship in addition to covering materials. Robust warranty specifications minimize long-term maintenance, extending your new concrete’s lifespan by as much as 50%.
Inquire about post-project support for extra peace of mind. Post-project support should be provided, as well.
Evaluate Local Project Experience
Consider the importance of local expertise. Contractors who know Palm Beach and Broward’s unique environment produce superior results by adapting materials and methods to local conditions.
Check references on similar projects they have completed to ensure they will be the best fit to serve your needs.
Customer Success Stories
Customer testimonials are essential for establishing trust—especially for local concrete resurfacing services. They offer concrete evidence of quality and reliability, demonstrating proven results in the real world rather than just theoretical guarantees.
By sharing these success stories, we highlight not only the craftsmanship involved but the satisfaction and confidence of our clients. These stories are invaluable in showing the impact and value of the great work we do, and in forging genuine relationships with prospective clients.
Project Showcase: Palm Beach
Among those achievements in Palm Beach was resurfacing a 1,500 sq-ft residential pool deck. The largest challenge they faced was repairing extensive wear that had been created by years of exposure to saltwater and UV rays.
We extended the life of the surface with multiple layers of long-lasting overlays and a unique light-gray color finish. This method provides safe slip resistance and continuous long-term durability.
The homeowner was astonished by the simplicity of the process that led to their deck’s beautiful fit with their property’s coastal style.
One of those projects even resurfaced the individual driveways of a private gated community. Cracks and repairs were made with advanced methods, then a stamped surface was added giving the sidewalk a decorative look that sharply improved the streets’ aesthetics.
Residents appreciated the efficient timeline and the low-disruption approach, with several noting how the updated surfaces boosted the neighborhood’s appearance.
Project Showcase: Broward
In Broward County, we re-envisioned the patio of a busy commercial tenant space. To meet these design criteria, the client requested a modern, polished aesthetic, which was developed through decorative resurfacing with a faux-stone design.
The public response focused on the new, relaxed atmosphere, which helped lure people back into the shop.
One such residential project included a 2-car garage floor. The application of an industrial grade Acrylic coating made them durable enough to withstand heavy use while creating a dramatic aesthetic improvement.
The homeowner experienced an 89% increase in home value after their renovation.
Testimonials and Feedback
-
“The resurfacing exceeded my expectations—flawless work!”
-
“Professional and punctual team. My patio looks brand new!”
-
“They truly listened to our needs and delivered beyond.”
-
“Affordable yet premium results. Highly recommend them!”
Common threads are demonstrated quality, professionalism and the projects’ transformative nature. Feedback is a constant improvement cycle that’s led us to improve production and learn the best techniques to serve our community of listeners.
Conclusion
Concrete resurfacing provides an economical solution to restore and preserve your worn surfaces in Palm Beach and Broward. It increases function and adds aesthetic appeal, making it the perfect resurfacing solution for residential and commercial properties. When mastered techniques are applied and with maintenance, resurfaced concrete can last for decades, making it an economical choice. Local factors such as weather or changing regulations might come into play, having intentional planning up front helps to avoid derailment.
The right contractor makes for an ideal project, collaborating with you to mitigate concerns as they arise without compromising results. Whether it’s a residential driveway, patio or complex commercial environment, resurfacing provides benefits with beauty, value, and long-lasting performance. Begin your search and find something that meets your unique needs and budget. Reach out to concrete contractors and other experts in your community to start planning your project. Find out how resurfacing can work some serious magic on your home!
Frequently Asked Questions
What is concrete resurfacing?
Concrete resurfacing is a procedure in which an experienced contractor either repairs or entirely renews existing surfaces. The process is fairly straightforward—you just install a new layer of material on top of the current surface. This improves its aesthetic, durability and usability characteristics without the need for complete replacement.
What are the benefits of concrete resurfacing?
Not only is resurfacing a more affordable option than concrete replacement, it helps improve your property’s curb appeal and prolong the life of your surfaces. Plus, it’s perfect for these surfaces in Palm Beach and Broward’s hot sunny climate.
How long does concrete resurfacing last?
With good maintenance, resurfaced concrete can last 10–15 years or longer. Weather, use and the way that any material goes down, including the materials themselves affect how long it lasts.
Is concrete resurfacing cost-effective?
You’re right, resurfacing is a lot less expensive than concrete replacement. Not only does it beautify and increase its usefulness, it’s a smart investment.
How do I maintain resurfaced concrete?
Prevent it from becoming dirty in the first place by sweeping and washing periodically. Seal the surface every couple of years to keep it safe from erosion, weather, and staining, which is especially important in Florida’s humid climate.
How do I choose a qualified contractor?
Seek out licensed, insured professionals with strong reviews and a background in concrete resurfacing. Request references and a written, detailed estimate to determine a contractor’s reputation and commitment to quality work.